Virginia Tech faculty among team that was awarded new grant for fundamental innovation in building design
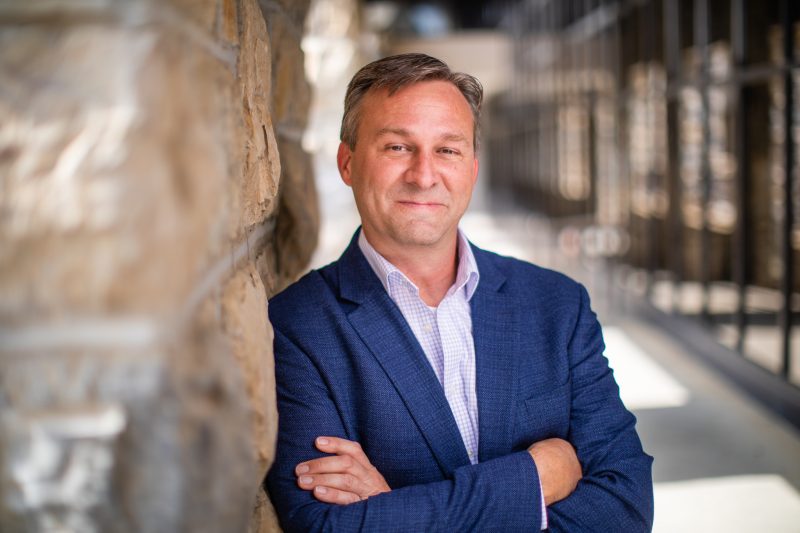
From a story posted by Northeastern University College of Engineering at Hajjar and Collaborators Awarded New Grant for Fundamental Innovation in Building Design - Northeastern University College of Engineering.
In a new grant from the Charles Pankow Foundation and industry partners, CDM Smith Professor and Northeastern Civil and Environmental Engineering Department Chair Jerome Hajjar and colleagues at three other institutions were awarded $425,000 to investigate a new modular steel plate floor framing and diaphragm system in steel building structures. The grant represents the first in a potential four-phase multi-year project. The Pankow Foundation, which was begun by noted industry leader Charles Pankow, is focused especially on taking research to practice with projects targeted for structural designers and the construction industry. The grant includes funding from industry partners, including the American Institute of Steel Construction (AISC), the MKA Foundation, Nucor Corporation, and Schuff Steel Company, with in-kind support from several additional organizations. Prof. Hajjar is joined on this project by Prof. Benjamin Schafer at Johns Hopkins University, Prof. Matthew Eatherton at Virginia Polytechnic Institute and State University, and Dean Sam Easterling and Dr. Onur Avci at Iowa State University. The team is working closely with Ron Klemencic and others at Magnusson Klemencic Associates, and with other industry representatives.
This project envisions a new structural system for steel buildings. The idea involves constructing steel floors in modules in fabrication shops, shipping them to the site, and lifting them into place within the structure. “The key feature is related to the AISC’s Need for Speed Initiative,” explained Hajjar. “We are looking to reduce the time it takes for design and construction of typical steel structures. By creating modules, we can regularize both the fabrication and transport of the steel and facilitate a streamlined construction process.” The modules use a solid steel plate and thus do not require the use of concrete. Concrete lengthens the time of construction, as it cannot be cast until the steel floor framing is in place, and builders must wait for the concrete to cure and harden. It also increases the weight of the building and limits the use of the floor for electrical, ventilation, and water piping systems. Concrete requires the transportation of heavy sands and mixing ingredients, which increases the carbon footprint of a building. “The system could also utilize 100% recycled steel, potentially made from steel mills powered by renewable energy, thus even further limiting the contributions of steel structural systems to climate change,” said Hajjar. The faster construction times would enable companies to build quicker, decreasing costs and speeding the time to occupancy.
In the first stages of this project, Hajjar and his team of collaborators will combine both computational simulation and experimental testing to understand how their new design will behave within the larger steel structure. This will involve understanding how the modular floor design reacts under severe wind, earthquakes, extreme loads, and vibration. The team is conducting vibration tests, acoustic tests, and tests of the structural system subjected to extreme loads. Recently, Hajjar and the project team completed a multi-year study on the behavior of traditional steel/concrete composite floor diaphragms in seismic zones. Using the insights from that project, he is studying the behavior of the proposed steel system to optimize the opportunities for achieving a cost-effective sustainable system that dramatically decreases the speed of construction of steel building structures.